RST Engineering's record success is powered by Sodick machinery and Sodi-Tech's exceptional aftersales support
RST Engineering, which currently has six Sodick EDM machines on-site at its manufacturing facility in Leighton Buzzard, reports that 2022/23 was the best year in the company’s history. The business bases this success not just on its commitment to ongoing investment in the latest Sodick machines, but in the backup and support of exclusive UK distributor Sodi-Tech EDM, which has been providing impeccable servicing, calibration, spare parts, consumables and applications advice since RST invested in its first Sodick machine back in 1996.
Robert and Maureen Taylor founded RST Engineering in 1986. Today, sons Jason, Sean and Paul help ensure the company continues to foster its reputation as a progressive and ambitious precision engineering business, and with good effect. RST bounced back strongly following the pandemic, during which the company invested in two Sodick machines: an ALC600G high-precision wire EDM with linear motors; and an AG80L die-sink EDM, the largest spark-erosion machine in their Sodick portfolio.
“We continue to invest in new Sodick machines because they play a big part in our success,” states Director Jason Taylor.
The 15-employee company serves numerous manufacturing sectors, but has a strong track record in scientific research and satellite communications.
“We currently have a scientific contract that runs continuously - 24/7 - on two of our Sodick wire EDMs, producing 1250 parts a week with tolerances down to 10µm,” explains Mr Taylor. “Hundreds of wire threads are required for each batch, and with the backup of consumables, spares and service from Sodi-Tech, the project runs flawlessly.”
The contract involves the manufacturing of two delicate mating components made from 316 stainless steel. One measures just 10mm x 2mm.
To keep the machines running continuously, RST Engineering relies on the wire, filters and resin consumables supplied by Sodi-Tech EDM, which also provides replacement wear parts such as guides and contact pick-ups.
“Sodi-Tech EDM has a huge stock of spare parts and consumables at its Warwick headquarters for all machines, and we always receive very prompt delivery,” states Mr Taylor.
RST Engineering runs six Sodick machines, three die-sink and three wire models. The company is currently considering trading in one of its older wire machines for another ALC600G, a model that is proving its reliability on the 24/7 scientific contract.
“At the weekend we set it going on Friday and it runs unattended until Sunday night with no unexpected stoppages,” says Mr Taylor. “Our approach is to set-up a double block of material, wiring in two directions to end up with 60 components per block.”
The company’s other recent investment is a Sodick AG80L die-sink machine which, with its 32-station toolchanger, was bought specifically for a project involving the manufacture of a satellite communications component. In total, RST Engineering had to produce 100 very large parts. Loading four at a time, each component required around 50 hours of spark erosion.
“As a project it ran seamlessly,” reports Mr Taylor. “In general, our investment in machining and inspection equipment always delivers an increase in accuracy, capacity and machining speeds, allowing us to keep up with demand for sophisticated parts like those for satellite communications systems, which are high in complexity and precision. We carry accreditations to both ISO9001 and AS9100D, while our inspection room is a temperature-controlled environment.”
Of course, with so much non-stop machining to incredibly high levels of precision, the law of averages says that sometimes there will be a setback. However, when this rare situation arises, Sodi-Tech EDM is always on hand.
“The support and back-up from Sodi-Tech EDM is fantastic, first by phone to see if they can get us up and running without having to dispatch a technician, providing advice and things to try,” says Mr Taylor. “That often resolves the issue, but if not, Sodi-Tech is fast at getting personnel on site. Furthermore, the skill set of their technicians is very high; they are all highly trained. I can’t fault them.”
Sodi-Tech EDM also services and calibrates all of RST Engineering’s Sodick machines on an annual basis. In fact, yearly machine calibration is an actual requirement of some RST customers.
As a final point, the company takes advantage of Sodi-Tech EDM’s application support if ever it encounters an awkward job and/or challenging material.
“If we want some advice or ideas, Sodi-Tech EDM is great at coming up with suggestions,” says Mr Taylor. “Overall, we have a fantastic working relationship with them. We bought our first Sodick machine in 1996 and never looked back. We can’t ask for more from the technology or the service we receive.”
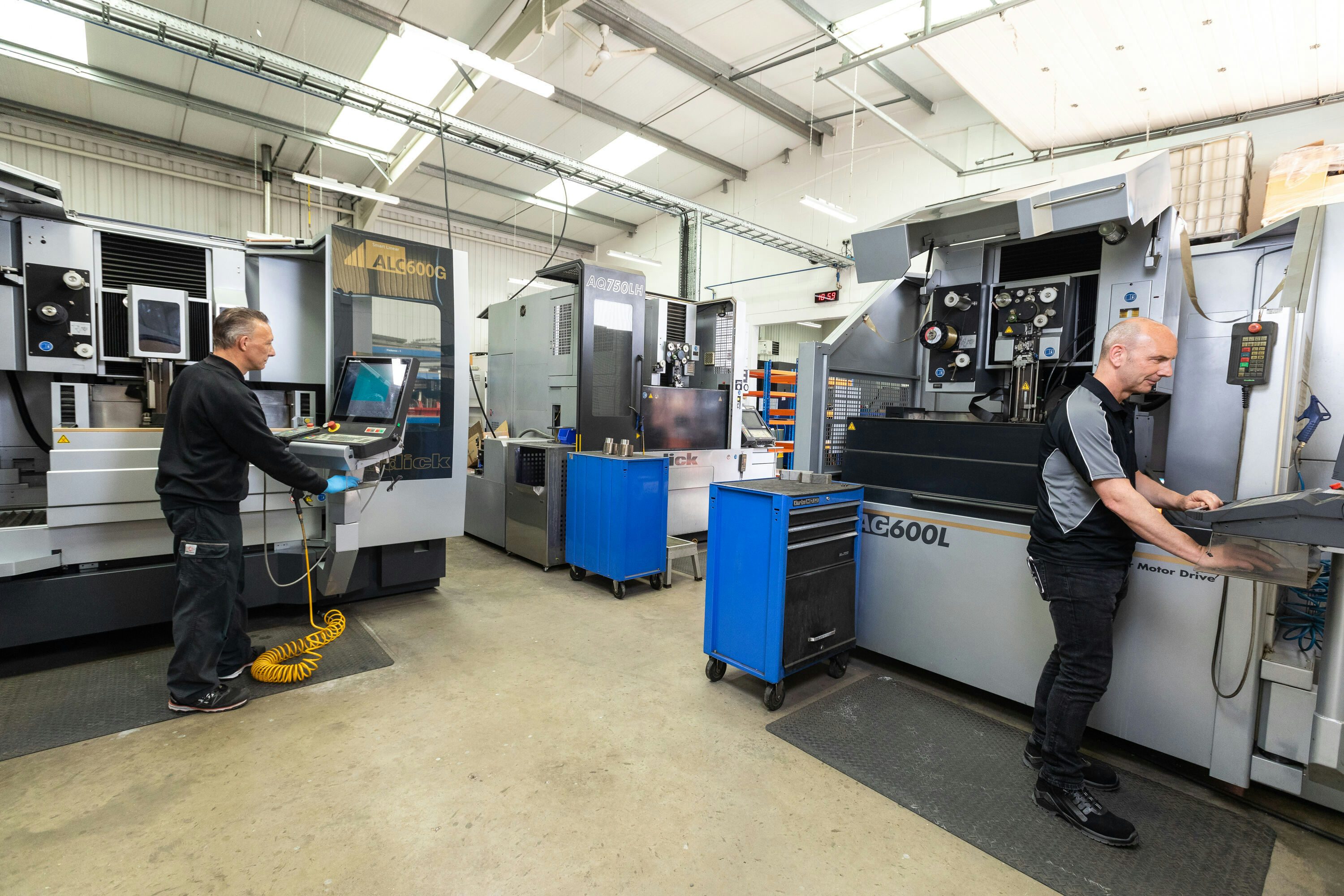
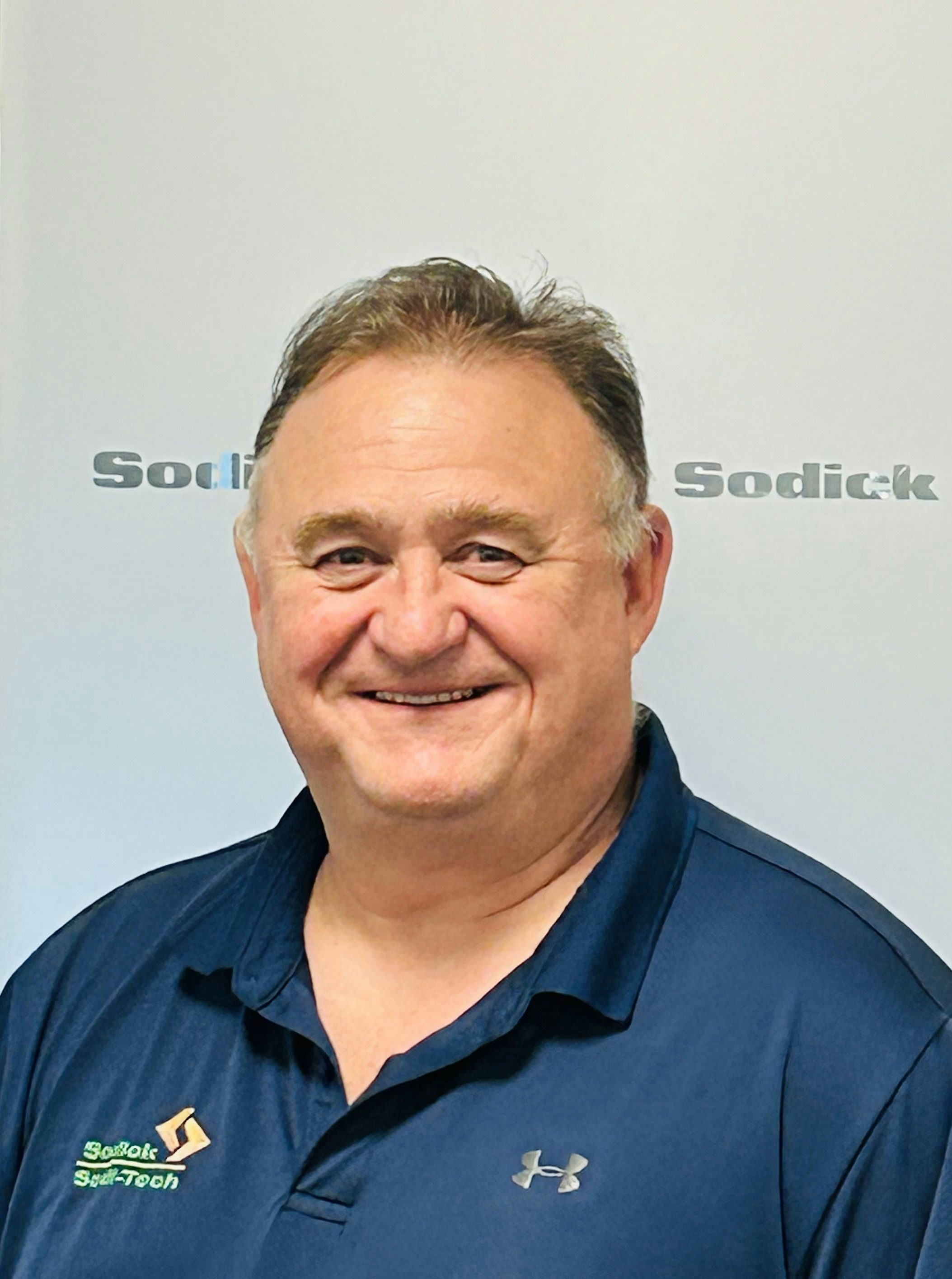
Sodi-Tech EDM Service and Technical Support
Aaron Holdstock, Sodick Senior Service Engineer, has been providing site service visits to RST Engineering for eight years. During this time, Sodick and RST Engineering’s relationship has developed into a valuable and reliable partnership as Aaron has aquired an in-depth understanding of RST Engineering’s working requirements, with the ability to carry out full machine services and calibrations, as well as deliver solutions both electronically (repair pc boards/modifications, programming logical control units) and mechanically.